

This is a situation where one turbo feeds another turbo, sharing the work of compressing the air across both compressors.
#Best turbo flutter series
At this power level, as stated above, it is a good idea to consider a series turbo application. There are, however, some general guidelines. Since this is a special case and there are so many ways to go about an ultimate power diesel application, it is not possible to cover it adequately in this article. The final case is the Competition category. With this, we can calculate Pressure Ratio ( ) using the equation. = Pressure loss due to Air Filter/Piping (psi).We will need to subtract the 1 psi pressure loss from the ambient pressure to determine the Compressor Inlet Pressure (P1). Also, we are going to assume that we are at sea level, so we are going to use an ambient pressure of 14.7 psia. In the Pressure Ratio discussion earlier we said that a typical value might be 1 psi, so that is what will be used in this calculation. To get the correct inlet condition, it is now necessary to estimate the air filter or other restrictions.
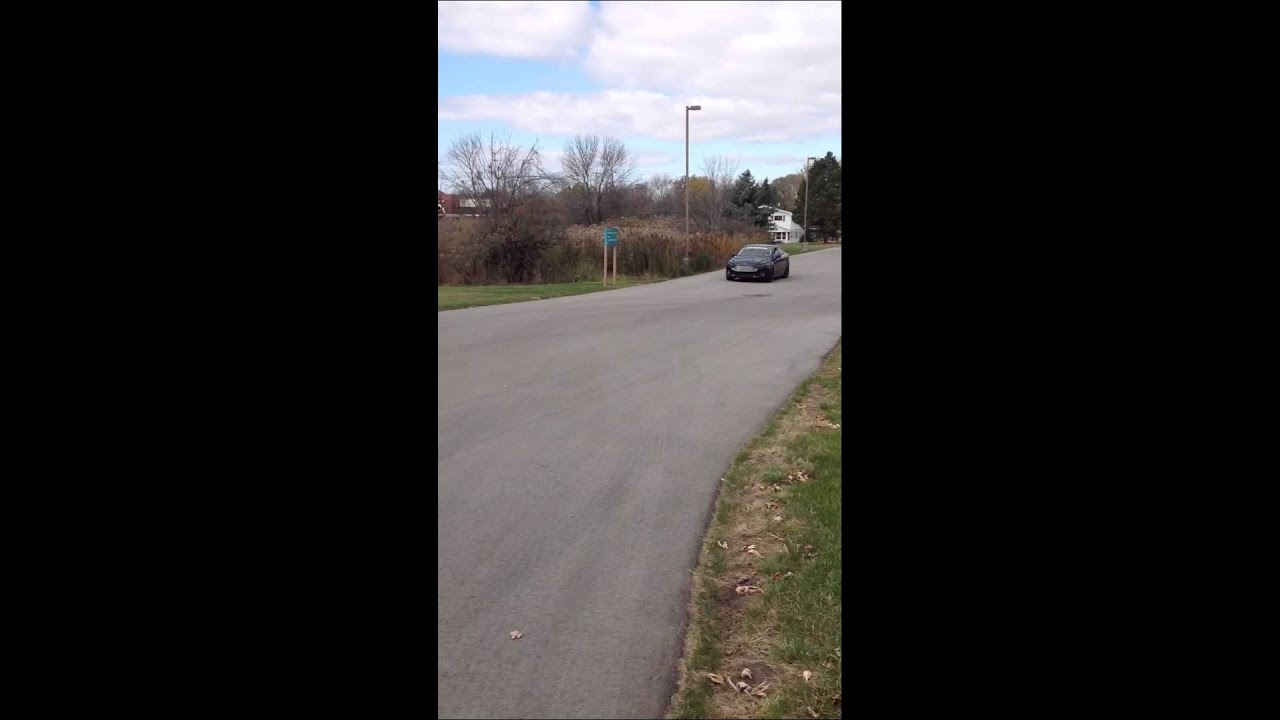
= Pressure loss between the Compressor and the Manifold (psi).MAP = Manifold Absolute Pressure (psia).P 2c = Compressor Discharge Pressure (psia).Therefore we will need to add 2 psi to the manifold pressure in order to determine the Compressor Discharge Pressure (P 2c). For our examples we will estimate that there is a 2 psi loss. Depending upon flow rate and charge air cooler size, piping size and number/quality of the bends, throttle body restriction, etc., you can estimate from 1 psi (or less) up to 4 psi (or higher). The best way to do this is to measure the pressure drop with a data acquisition system, but many times that is not practical. Next step is to determine how much pressure loss exists between the compressor and the manifold. We are almost ready to plot the data on the compressor map. So now we have a Mass Flow and Manifold Pressure. = 34.5 psia (remember, this is absolute pressure subtract atmospheric pressure to get gauge pressure, 34.5 psia – 14.7 psia (at sea level) = 19.8 psig) Wa = 59.2 lb/min as previously calculated.
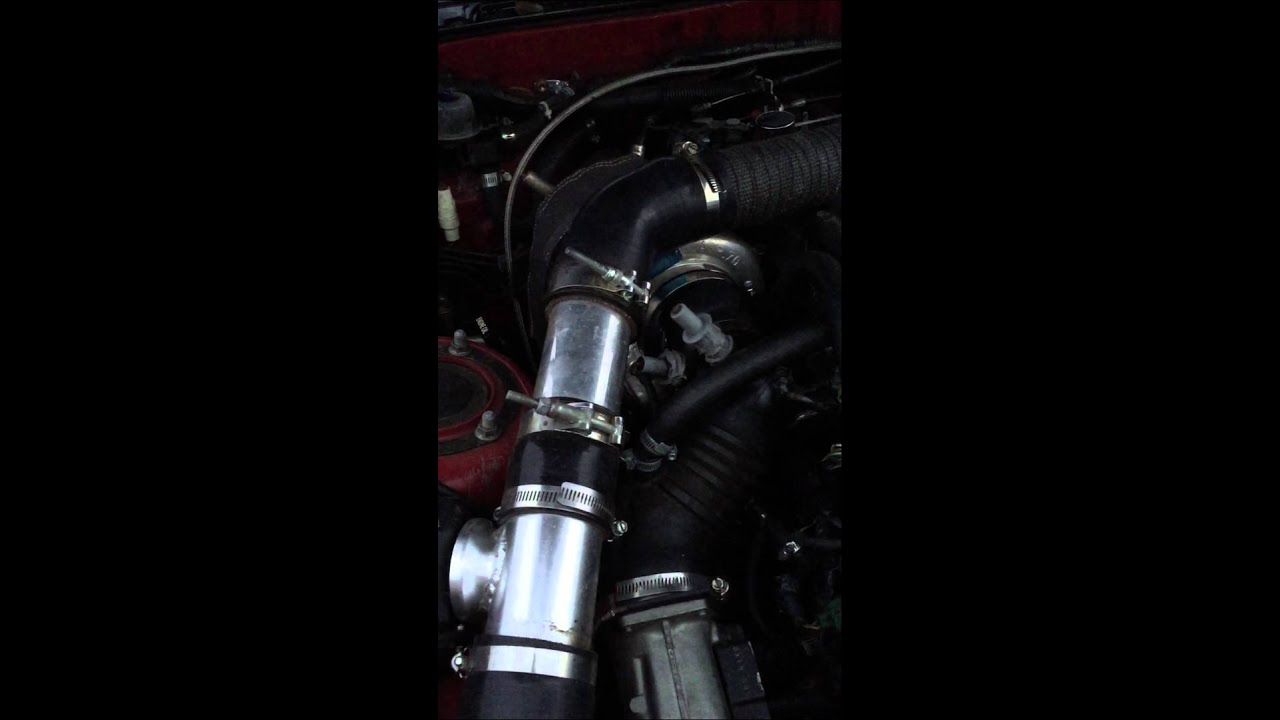
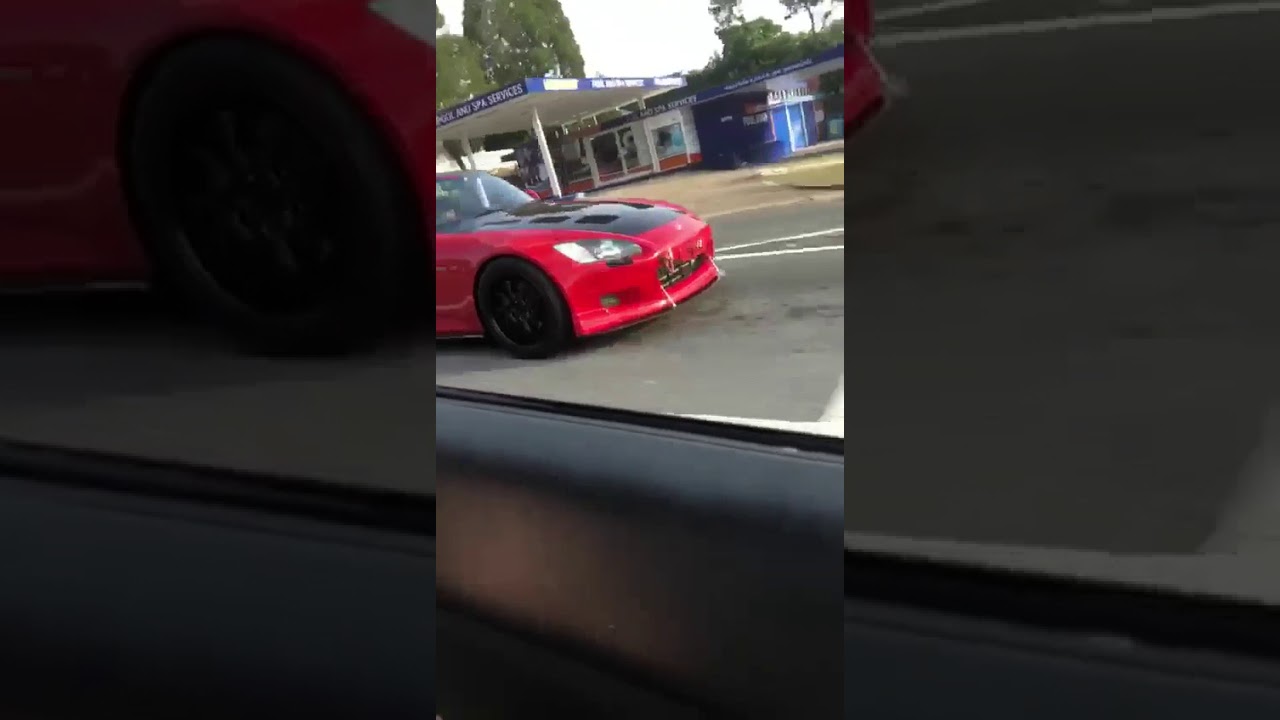
I would like to make 425 wheel hp an increase of 150 wheel horsepower. I have a 6.6 liter diesel engine that makes a claimed 325 flywheel horsepower (about 275 wheel horsepower as measured on a chassis dyno). Since turbochargers are sized by how much air they can deliver and airflow is proportional to engine power, a realistic horsepower goal is critical to make the right choice. In order to decide on the appropriate turbocharger for your diesel engine, the very first thing that needs to be established is the power target. When the modifications get more serious, a bigger turbo is a must have to compliment even more fuel.
#Best turbo flutter upgrade
With an upgrade turbocharger selected to compliment the extra fuel, smoke is drastically reduced, EGT’s are under control and, since the turbo is operating in a more efficient range, horsepower and drivability are enhanced. Under these conditions, the stock turbo is running on borrowed time.
#Best turbo flutter driver
Under heavy acceleration, smoke is pouring from the tailpipe as the EGT’s and turbo speeds are climbing into the danger zone requiring a prudent driver to back off the accelerator pedal early to keep from damaging the engine. This can usually be seen on an engine with a performance chip (at the highest power setting) and maybe an intake or exhaust upgrade. The lower efficiency means that more turbine power is required to reach the same boost causing higher back pressure in the exhaust manifold.
